Growth is a natural aspiration for any business owner. And, if you run a small manufacturing company, you likely dream of the day when you can expand operations, increase production, and cater to a larger market.
However, scaling a manufacturing business comes with its unique set of challenges. Research suggests that only 22% of businesses launched in the past ten years have successfully scaled.
If approached without a structured plan, the scaling process can lead to oversights, inefficiencies, and unexpected costs. Here’s your guide on the key considerations to keep in mind as you scale your manufacturing company.
Understand Your Current Capacity
Before you even think about scaling, have a clear picture of where you currently stand. Examine your existing machinery, tools, and equipment. Can they handle increased demand or do you need to invest in new technology? Do you have enough skilled labor to handle an increase in production? If not, consider hiring or training.
Don’t neglect the financial aspect of scaling, either. Use past sales data, market trends, and customer feedback to predict future demand. This will help in determining how much you need to scale. This includes costs related to new machinery, additional staff, infrastructure upgrades, and increased inventory.
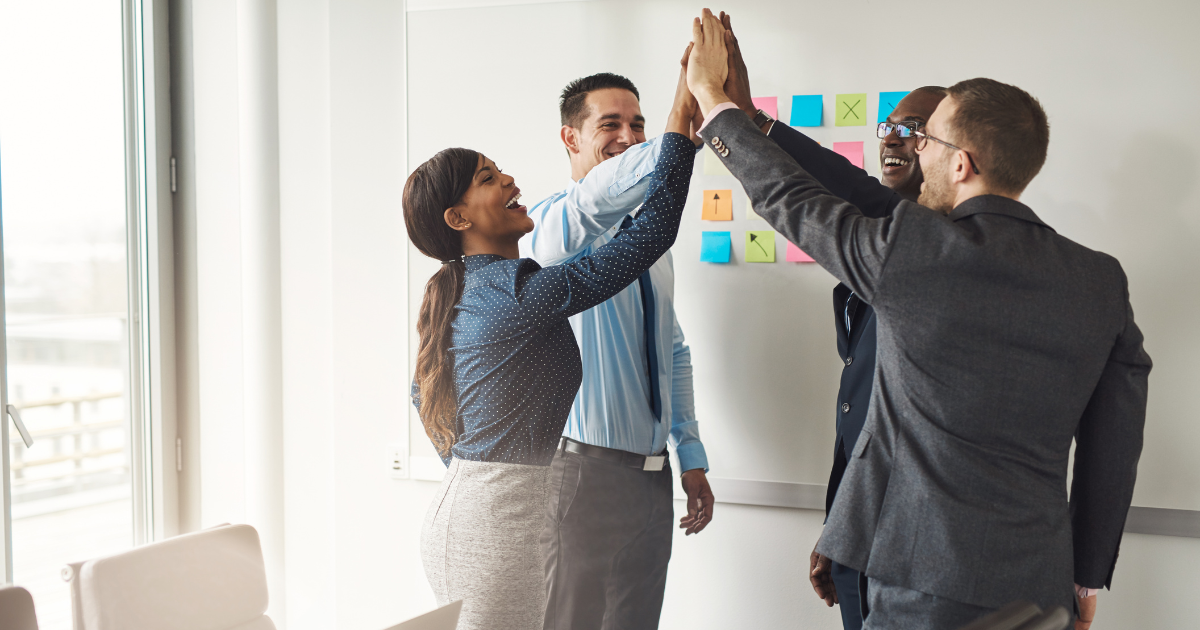
Focus on your People
An indispensable component of scaling your manufacturing business is a robust Human Resources (HR) management system. As your operations grow, so will your team, and effectively managing human capital becomes a critical factor in achieving your expansion goals.
Recruitment and Retention
Recruiting the right talent and retaining them is foundational to your business growth. A strong HR department will help in identifying, attracting, and retaining skilled individuals who align with your company’s culture and objectives. Additionally, competitive compensation and benefits, clear career progression paths, and a positive work environment are crucial for employee retention.
Training and Development
A well-informed team is the backbone of any successful manufacturing enterprise. Make sure your people are up to speed in these areas:
- Industry Trends: The manufacturing sector is constantly evolving. Regular training sessions can ensure that your team is acquainted with the latest methodologies, tools, and industry best practices.
- Adapting to New Technology: Whenever a new technology is integrated, tailored training programs ensure that the team can leverage these tools effectively, maximizing ROI.
- Soft Skills Development: Technical know-how is vital, but soft skills like problem-solving, communication, and team collaboration are equally important. Regular workshops can hone these skills, ensuring a holistic approach to professional development.
Legal Compliance and Employee Relations
As your business grows, adhering to labor laws and regulations becomes increasingly complex. An effective HR management system helps in navigating through various legal compliances, including safety regulations, equal employment opportunity laws, and others. Additionally, HR plays a vital role in managing employee relations, resolving workplace conflicts, and fostering a positive work culture.
Performance Management
Performance management systems help in setting clear expectations, monitoring performance, and providing regular feedback. This systematic approach ensures that your employees are aligned with your business goals and are contributing positively towards achieving them.
Employee Engagement and Wellbeing
Engaged employees are more productive and contribute more positively to the company’s culture and goals. HR programs that focus on employee engagement, recognition, and well-being can have a significant positive impact on the morale and productivity of your workforce.
By investing in a strong HR management system, you can ensure that your business is well-positioned to attract and retain the talent needed to scale effectively. Moreover, it creates a structured framework to manage and support your growing team, making your manufacturing business more resilient and better equipped for sustainable growth.
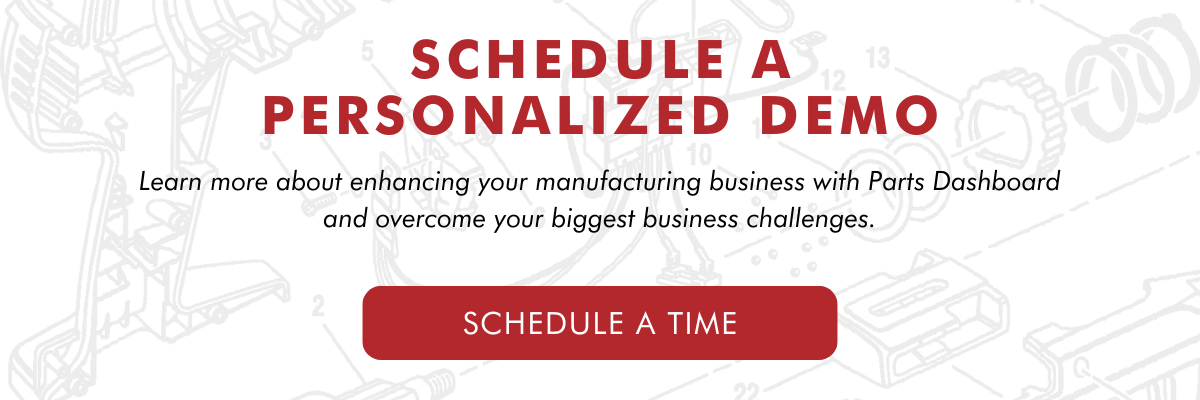
Invest in Technology
The contemporary manufacturing landscape is filled with technological solutions tailored to address specific challenges and enhance growth:
- Inventory Management Software: Managing inventory efficiently is crucial for manufacturing operations to prevent overstocking or understocking, which could lead to delays or financial losses. Inventory Management Software, like Parts Dashboard, provides a centralized platform to track, manage, and optimize inventory levels in real-time. It can automate ordering processes, monitor supply levels, and provide analytics to foresee demand, ensuring a smooth flow of materials and finished goods.
- Product Lifecycle Management (PLM) Systems: PLM systems oversee the lifespan of a product from its conception through design and manufacture, to service and disposal. They centralize product information, streamline process management, and foster collaboration among various stakeholders. By managing product-related data, and integrating with other enterprise systems, PLM helps in accelerating product development, improving product quality, and reducing production costs.
- Quality Control Technology: Ensuring a consistent product quality, especially during periods of rapid expansion can be a tough nut to crack. Quality control technologies, like automated inspection systems, can provide real-time feedback, thereby ensuring that standards are upheld regardless of volume escalations.
- Communication Tools: As teams grow and operations morph into more complex structures, communication becomes more important. Investing in unified communication tools guarantees that teams, whether situated on the shop floor or holding managerial positions, remain interconnected and well-informed, promoting a culture of transparency and swift decision-making.
- Operations and Management Software: Your operations and management software can make or break your scaling process. Look for:
- Real-Time Analytics: To monitor operations and make data-driven decisions.
- User-Friendly Interface: Your team should spend time on production, not deciphering complicated software.
- Scalability: Ironically, your scaling tool should itself be scalable. As you grow, it should adapt.
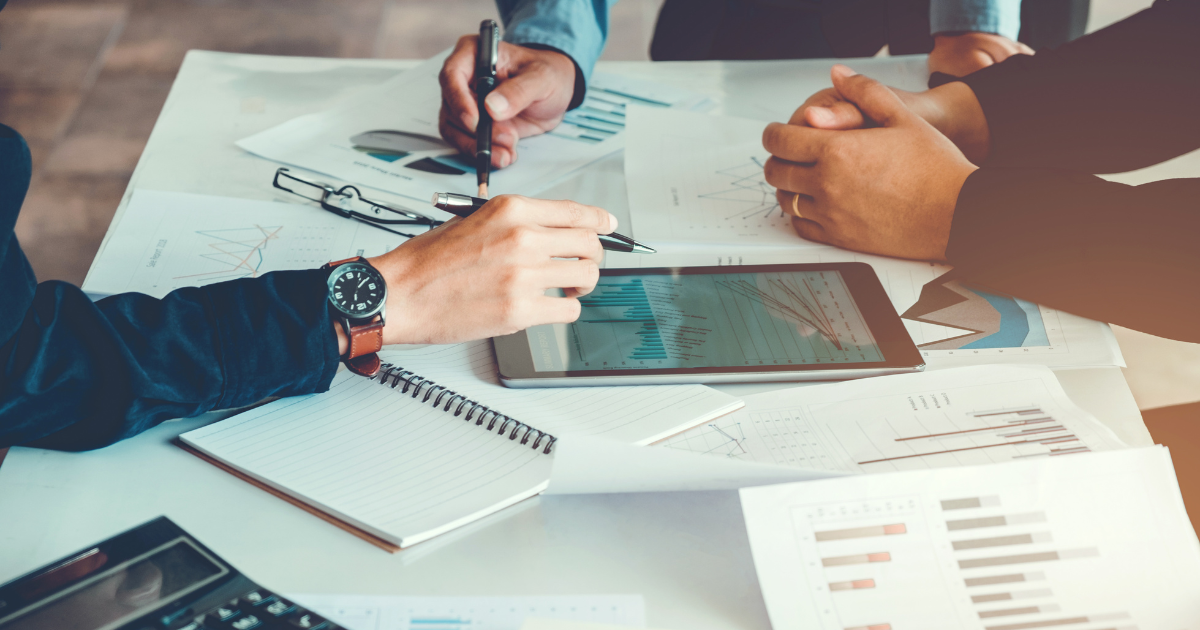
Strategize to Mitigate Risks
Scaling a manufacturing business offers a multitude of opportunities, but it also introduces potential risks. Rapid growth, if not managed adeptly, can result in operational inefficiencies, miscommunication, and even non-compliance with industry regulations. To circumvent these pitfalls, strategic actions are needed.
Effective growth is often a result of foresight paired with meticulous planning.
- Periodic Business Plan Revisions: A static business plan may quickly become outdated in a rapidly evolving environment. It’s essential to revisit and modify your business plan periodically, ensuring it reflects the current market conditions, internal capabilities, and long-term aspirations.
- Anticipate Challenges: Growth invariably introduces new challenges. Predictive analytics and forecasting tools can provide insights into potential roadblocks. By proactively identifying these challenges, businesses can devise strategies to tackle them before they escalate.
- Align Resources: As your business grows, resource allocation becomes even more critical. Planning ensures that both human and capital resources are distributed optimally, catering to the business’s immediate and future needs.
By embracing these strategies manufacturing businesses can chart a course for growth that is both ambitious and risk-averse.
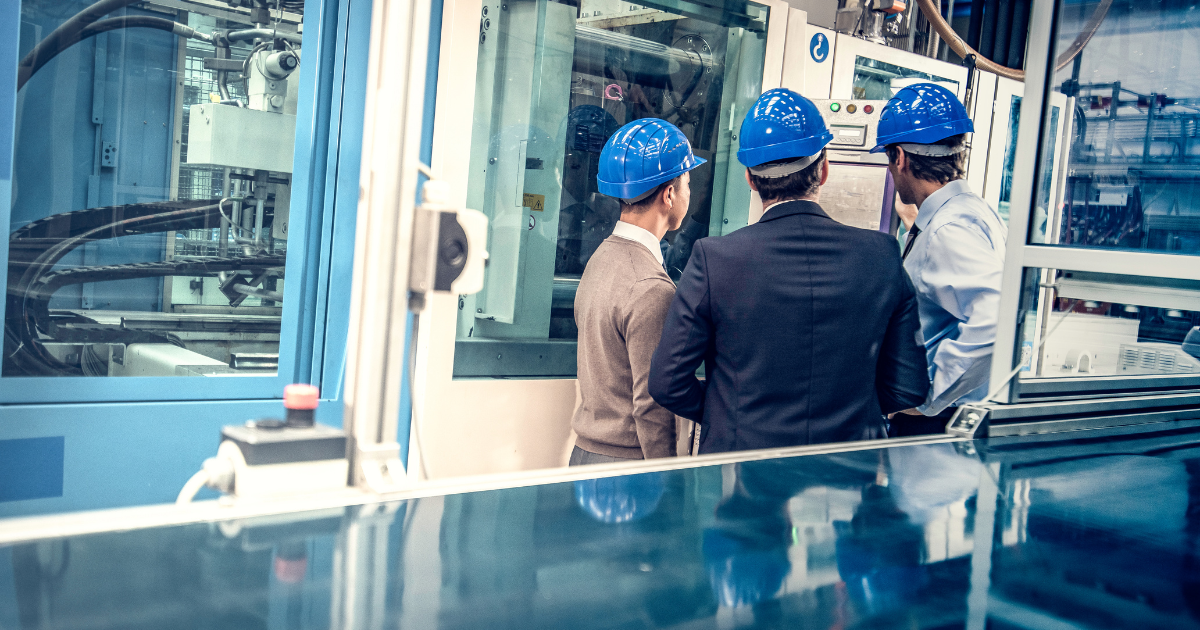
Other Considerations for Scaling Up
Beyond understanding your capacity, focusing on your people, investing in tech, and risk mitigation, there are a few more items to consider when scaling up your manufacturing company. So, what should be on your checklist?
Navigating the World of OSHA and EEOC
As you add more members to your team and increase your production, adhering to safety regulations becomes paramount. The Occupational Safety and Health Administration (OSHA) ensures safe working conditions, and you’ll want to be on their good side. Regular safety audits, employee training, and maintaining a safe environment will be key.
Furthermore, as you hire, ensure you’re practicing non-discrimination. The Equal Employment Opportunity Commission (EEOC) oversees this, so familiarize yourself with their guidelines. This not only ensures you’re compliant but also fosters a diverse and inclusive workplace.
Streamlining Operations: The Role of SOPs in Scaling
Standard Operating Procedures (SOPs) are the backbone of any successful manufacturing operation. They provide a clear roadmap for tasks, ensuring consistency and quality. As you scale:
- Review and Revise Existing SOPs: Your old SOPs might not cater to your new scale of operations.
- Implement New SOPs: New machinery? New department? They’ll need their SOPs.
- Regularly Audit and Update: As you grow and the industry evolves, your SOPs should too.
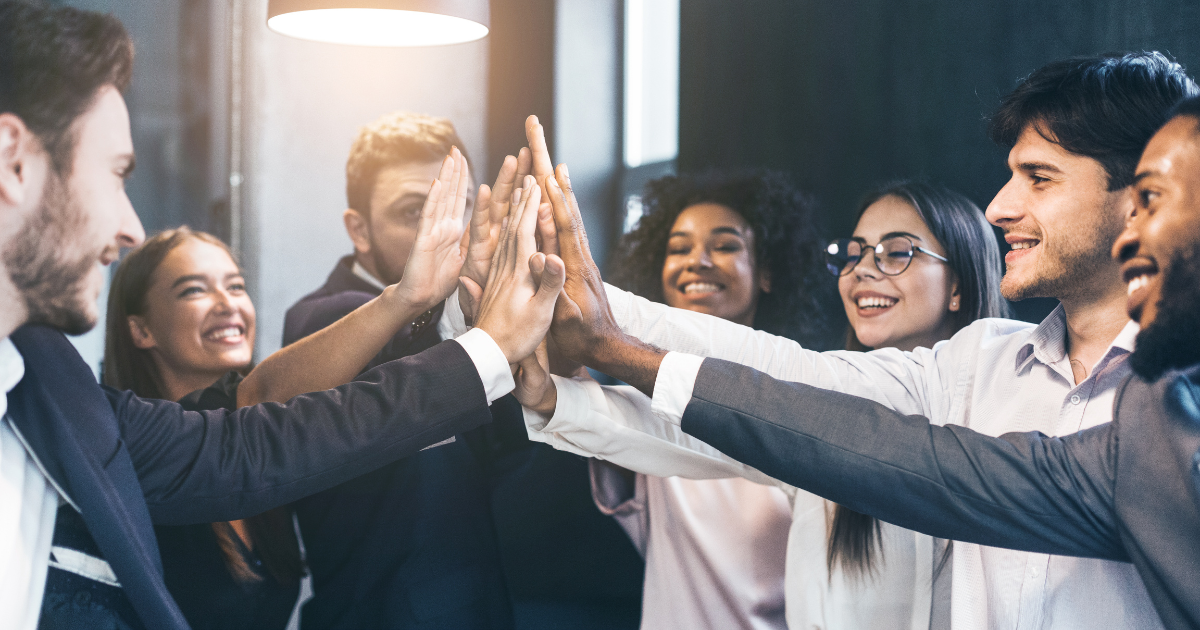
Scaling Successfully in Manufacturing
Scaling in the manufacturing sector demands a blend of strategy and execution. By integrating technology, following best practices, and staying compliant, you can achieve seamless and sustainable growth.
The considerations and strategies laid out in this guide are meant to serve as pillars, supporting your journey as you expand your horizons. As you scale, let strategy, foresight, and adaptability be your guiding lights, ensuring not just growth, but sustainable and meaningful evolution for your manufacturing business.
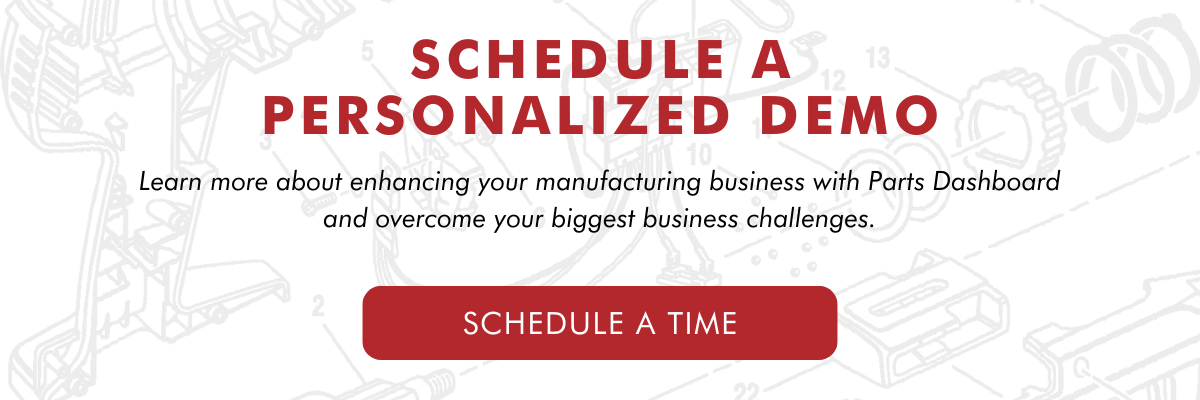