In manufacturing, accurate cost tracking is not just about maintaining budgets; it’s about gaining a competitive edge through better pricing and improved profitability. This is where job costing, an essential accounting method, comes into the picture. It’s specially designed for industries like manufacturing where work is carried out in distinct, identifiable units.
Understanding Job Costing in Manufacturing
Job costing involves tracking the expenses and revenues of individual jobs or projects, thereby calculating each job’s overall profitability. It’s characterized by three key elements:
- Labor Costs: This encompasses all the labor costs directly linked to a job. It involves tracking the time and effort of workers directly involved in the manufacturing process, ensuring that labor expenses are accurately attributed to each job.
- The Cost of Materials: These are the raw materials and components used in the manufacturing of a product. Tracking the cost of materials is vital for understanding the direct expenses incurred in the production process of a job.
- Allocation of Overhead Expenses: This includes all the indirect expenses that are not directly tied to a specific job but are necessary for the overall operation. Costs such as factory rent, utilities, and equipment depreciation.
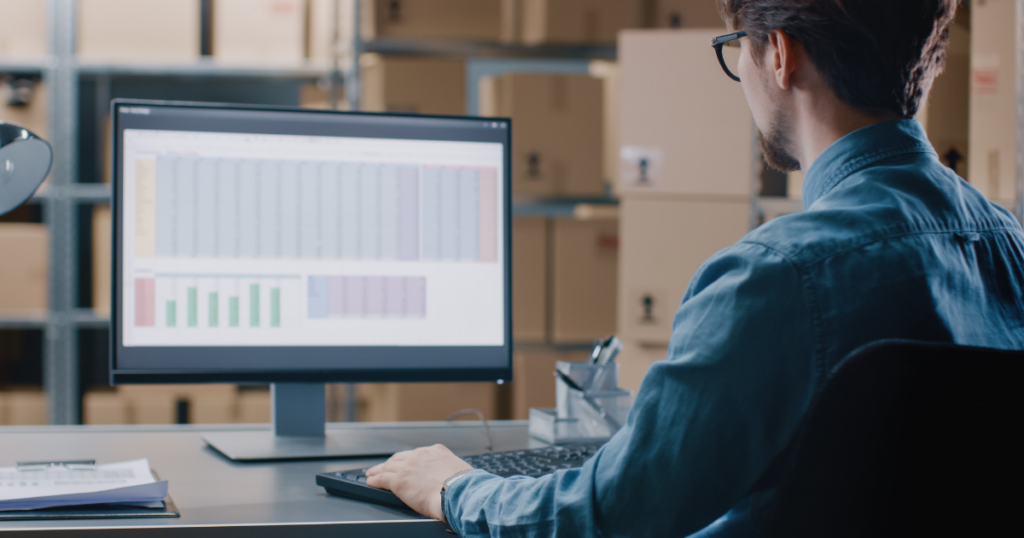
The Traditional Approach: Spreadsheets and BOM
Traditionally, you might use spreadsheets to track the Bill of Materials (BOM) and other costs. In a spreadsheet, you list all materials, labor, and overheads, assigning them to specific jobs.
But there’s a catch – this information often stays local to that sheet. When it comes to updating costs like standard labor rates, you find yourself stuck in a loop of manual updates across multiple files.
Here are a few more challenges you may face:
- Error-Prone Data Entry: Manually entering data in spreadsheets can lead to errors, such as typos or incorrect formula use. These errors can significantly impact your cost calculations and materials requirements.
- Lack of Real-Time Updates: Spreadsheets typically don’t update in real-time. This can make it challenging for you to keep track of changes in material costs and availability, potentially resulting in decisions based on outdated information.
- Limited Scalability: As your business grows, so does the complexity and volume of data in your BOM. Spreadsheets may become cumbersome and inefficient for managing large amounts of data, impacting your productivity and increasing the risk of errors.
- Difficulty in Collaboration: Collaborating on a spreadsheet, especially when multiple departments are involved, can be challenging for you. Issues with version control can arise, making it hard to track who made specific changes and when.
- Lack of Integration with Other Systems: Your spreadsheets might not integrate well with other systems like ERP (Enterprise Resource Planning) or MRP (Material Requirements Planning). This lack of integration can lead to isolated information and inefficiencies in data transfer.
- Inadequate Reporting and Analysis Capabilities: While spreadsheets offer basic reporting functions, they may not be capable of handling the complex analyses you need for effective manufacturing cost management, like predictive analytics or trend analysis.
- Security and Data Integrity Risks: You could face security risks, such as unauthorized access or data corruption, with spreadsheets. Maintaining data integrity can also be a challenge, especially in a multi-user environment.
- Time-Consuming Maintenance: Maintaining and updating complex spreadsheets can be time-consuming, diverting valuable resources from other critical tasks in your business.
Due to these challenges, you might consider moving towards more specialized software solutions that are designed to handle the complexities of BOM and manufacturing cost management more efficiently and effectively. Not to toot our own horn, but a specialized solution like Parts Dashboard may just do the trick for you.
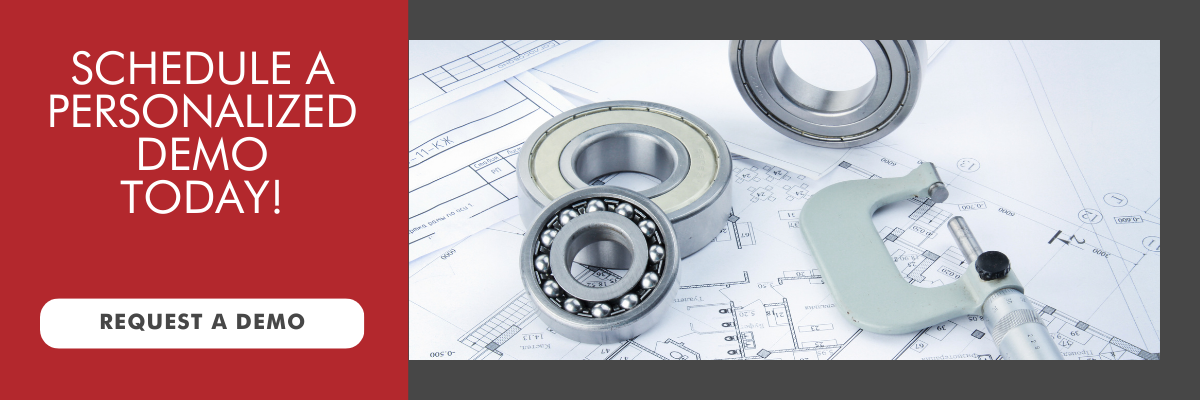
Enter Parts Dashboard: A Game Changer
Now, imagine a system that not only simplifies this process but makes it more dynamic. Parts Dashboard is a product lifecycle & inventory management system designed to keep your costs current and your processes streamlined.
With Parts Dashboard, when you update a cost element like labor rates, it feeds throughout the software. Think of it as a master of all costs – change them once, and it reflects them everywhere!
Organizing and Streamlining
Parts Dashboard doesn’t just update costs dynamically. It allows you to organize and arrange everything into subgroups, activities, processes, and materials. This level of organization provides clarity and makes managing complex manufacturing jobs much more straightforward.
Access and Integration
With all your information in one place, accessible and up-to-date, you avoid the pitfalls of outdated or inconsistent data. This centralized approach ensures that everyone, from the shop floor to the top management, works with the same numbers and information.
Efficiency and Cost-Saving
By moving away from traditional spreadsheets to a more integrated system like Parts Dashboard, you save time and reduce errors. This efficiency translates into cost savings and better resource allocation, directly impacting your bottom line.
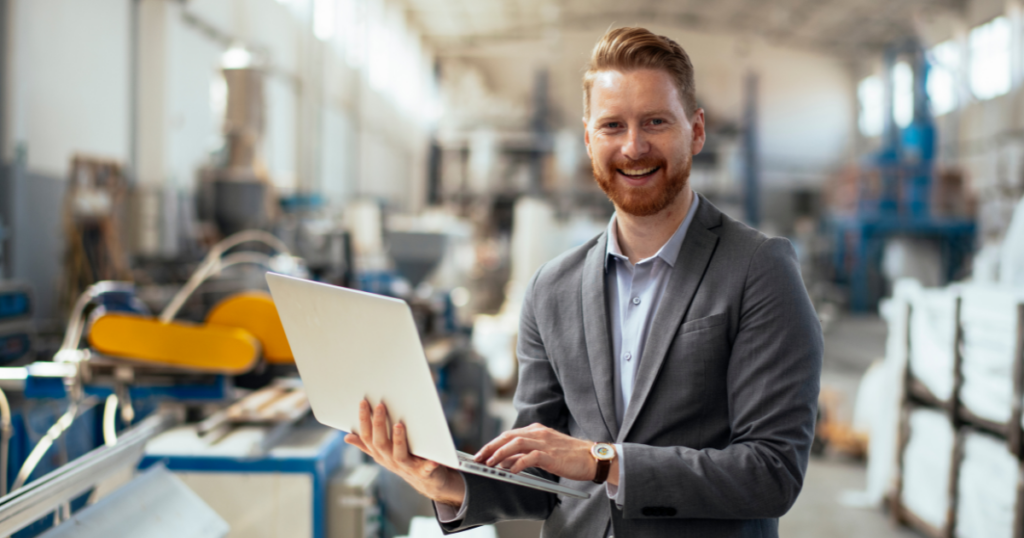
Embracing a New Era in Manufacturing Efficiency
Moving beyond traditional spreadsheets to a comprehensive system like Parts Dashboard represents a significant change in how you approach growth and efficiency in your manufacturing business.
This transition isn’t just about keeping your cost information current. It’s about embracing a holistic system that refines and streamlines every aspect of your production management. By making this change, you can greatly improve the accuracy of your material and cost tracking, leading to better decision-making.
Parts Dashboard provides you with robust features such as real-time updates, advanced analytics, and seamless integration with other enterprise tools. These capabilities create a more cohesive and efficient operational environment for your business.
Ultimately, making this strategic shift is a crucial step in driving your profitability, ensuring the long-term sustainability of your business, and maintaining a competitive edge in the ever-evolving manufacturing sector.
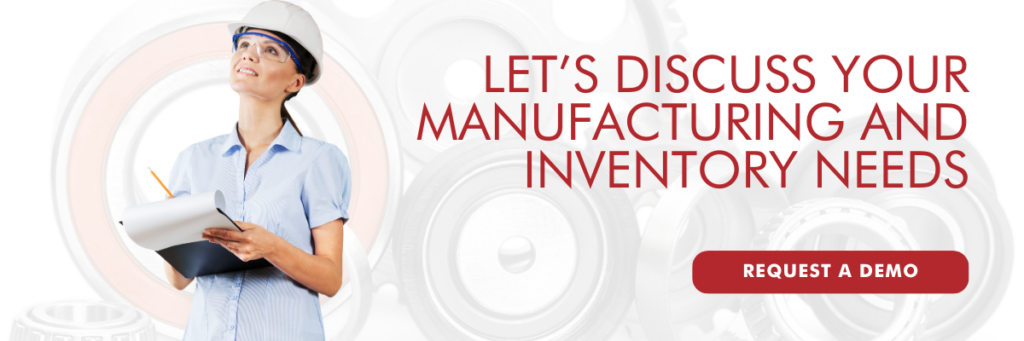